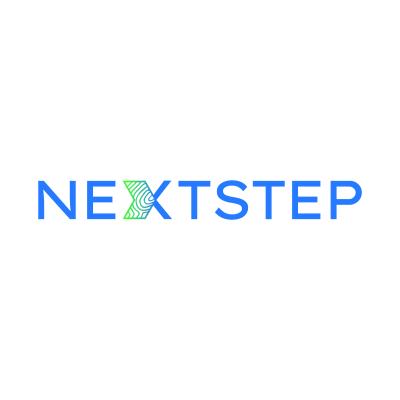
NEXT-STEP
NEXT-GEN OF SUSTAINABLE BIOBASED CHEMICAL PLATFORMS AND POLYMERS: ENHANCING SUSTAINABILITY IN EUROPEAN INDUSTRY
NEXT-GEN OF SUSTAINABLE BIOBASED CHEMICAL PLATFORMS AND POLYMERS: ENHANCING SUSTAINABILITY IN EUROPEAN INDUSTRY
Scaling up sustainable and biodegradable materials is crucial for the future advancement of European industry. Currently, many bio-based alternatives struggle to compete with established fossil-based chemicals due to challenges in environmental, economic, and societal performance. To overcome this, NEXT-STEP aims to build on the H2020 BioCatPolymers project to scale up and demonstrate a sustainable, safe, and economically viable production process for a new chemical platform with large-scale applications, notably in the bio-based polymer market.
By reducing manufacturing costs and using second-generation feedstocks such as hardwood sugars produced from sustainably managed forests, NEXT-STEP aims to develop a new chemical platform, the 3-methyl-d-valerolactone (3MdVL) that will improve the sustainability and recyclability of polyurethane (PU) products and unlock new engineering plastic applications for polylactic acid (PLA) co-polymers. This initiative seeks to address environmental concerns while fostering the adoption of bio-based materials in various industries.
The NEXT-STEP project addresses the pressing need for sustainable and biodegradable materials in European industry, by:
NEXT-STEP’s main target is to demonstrate and scale up a sustainable, resource- and energy-efficient route to produce 3MdVL, which is currently not commercially available at a large scale. Expected impacts include: