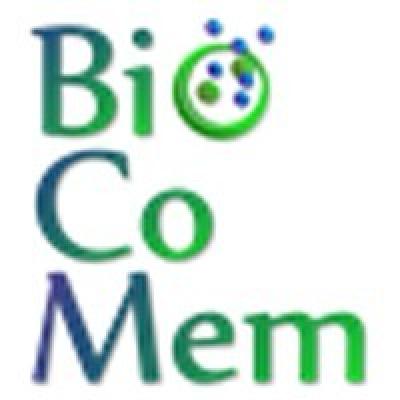
BIOCOMEM
Bio-based copolymers for membrane end products for gas separations
Bio-based copolymers for membrane end products for gas separations
The supply of many precursors and ingredients relies on chemical separation techniques to isolate the various components. Currently, many of these separation techniques rely on heat-based approaches, such as distillation. This currently amounts to around 10–15 % of the world's energy consumption, with the concomitant implications this has for GHG emissions.
Membrane-based separation techniques offer an alternative with the potential for far lower energy consumption. Wider adoption of these techniques would reduce GHG as a result. In addition, by using membranes manufactured from bio-based materials, it would increase overall sustainability and further reduce the environmental impact. However, such products need to be able to withstand long-term operation at temperature and pressure variations and prolonged contact with degradative substances. Such membranes require a complex structure that rely on highly specific methods of production. One aspect of this is the use of a hollow fibre. If these can be made by a spinning technique, it is more energy efficient and less likely to have defects. Current materials for membranes – polyether-block-amide copolymers (PEBAs) – are not ideal for this approach.
Therefore, the BIOCOMEM project will develop and validate gas separation membranes at TRL 5. These will use bio-based PEBAs that offer higher potential for processing as hollow fibres. The membranes will be specifically designed to improve gas separation performance, offer higher resistance to chemical attack, all while using an increased amount of bio-based material.
The overarching objective for the BIOCOMEM project is to demonstrate that membrane-based separation techniques using PEBA-type (Polyether block amide) copolymers are more efficient than their heat-based equivalent methods. This will reduce the overall environmental impact through a number of mechanisms.
With this, the BIOCOMEM project has three specific objectives:
By achieving its overall objectives, the BIOCOMEM project makes separation techniques more energy efficient, more sustainable and lessens their overall environmental impact.
In addition, it will also make contributions to specific BBI JU KPIs through:
In addition, the BIOCOMEM project will have a number of other positive impacts. It will improve the EU’s innovation capacity and knowledge integration. It will also bring a positive environmental impact. By using biomass as a feedstock (rather than fossil fuels) it will use renewable rather than finite resources. In addition, its CO2 filtering technology will prevent atmospheric release of this GHG.