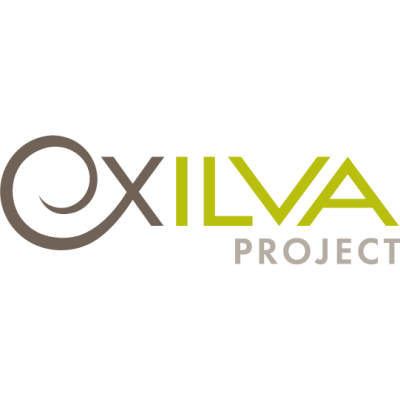
EXILVA
Flagship demonstration of an integrated plant towards large scale supply and market assessment of MFC
Flagship demonstration of an integrated plant towards large scale supply and market assessment of MFC
Micro fibrillated cellulose (MFC) is a revolutionary product with potential in a wide range of applications, including personal care, cosmetics, home care, pharmaceutical excipients, adhesives and sealants, composites and resins, agricultural chemicals, fish, bait, concrete, and CO2 capture. It also has the potential to replace many fossil fuel-based products.
However, the commercialisation of MFC has proved challenging, particularly in making industrial quantities with sufficient running efficiency and stability. In addition, drying the MFC fibres cost-effectively without losing significant performance is a major challenge.
The EXILVA project aimed to change this by transferring technology from the existing pilot production and eventually scaling up to commercial levels.
EXILVA has shown significant functionality in more applications than expected. In most of the cases, the dosage efficiency is better than expected.
EXILVA | BBI JU project
EXILVA's beneficiary Borregaard features from 8’ 44’’.