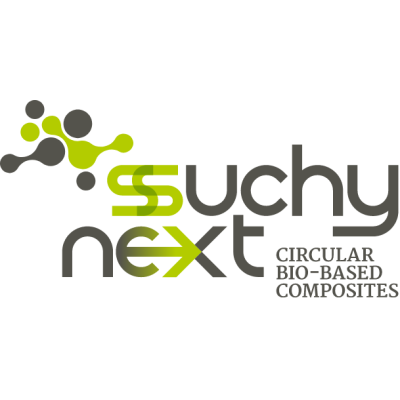
SSUCHY-Next
Developing the supply chains for industrial hemp fibre and bio-based resins towards high performance circular bio-based composites
Developing the supply chains for industrial hemp fibre and bio-based resins towards high performance circular bio-based composites
The SSUCHY-Next project builds upon its predecessor, SSUCHY, which developed the hemp fibre supply chain and bio-based epoxy resin. Recognising the need to advance beyond SSUCHY’s achievements, SSUCHY-Next seeks to elevate various aspects of the hemp fibre supply chain to TRL 7, a significant step towards industrial viability. This includes scaling up the production of hemp fibre products, from field extraction to composite materials.
SSUCHY-Next addresses the challenge of the limited availability of bio-based polymer matrices, crucial for sustainable composite production, by focusing on three bio-based polymer systems and aiming for high bio-content and recyclability: bio-based acrylic polymer ('Elium®') with very high bio-content, fully bio-based benzoxazine, and fully bio-based BG-epoxy, building upon the system developed in the first SSUCHY project.
The project aims to demonstrate the use and environmental benefits of the new bio-based polymer matrices in wind turbine blades, leather replacement materials, and construction materials, such as façade cladding panels. The project will pay particular attention to recyclability of the new materials and products, ensuring the sustainability of the bio-based solutions.
Through a series of focused objectives, SSUCHY-Next aims to revolutionise material performance and manufacturing processes, by:
Through rigorous monitoring and adherence to Open Science practices, SSUCHY-Next aims to maximise its impact and pave the way for a greener future in composite materials by: